 |
 |
PITONS, DIAMONDS, CLUBS AND SPADES
I was six years old when I designed my first ice tool. In one of my first primary school exercise books I found an old drawing which showed how to climb a mountain: ice axe in hand, wearing "things with nails" on my feet and a row of pitons placed close together... no doubt in my impressionable young mind I could still hear my Partisan grandfather's stories about how he would climb mountains in order to escape and hide from the enemy. His stories always included a certain Lieutenant Corbelli who would tell him to climb a wall or improvise using a double rope and when he mimed his climbs, he would wear enormous imaginary boots which he'd made out of bits of iron, string... and lots of imagination.
A bit of that same imagination obviously rubbed off on me when, a few years later, I built my first ice axe.
It weighed three kilos... not that it was very heavy... to be precise, it weighed 3000 and a bit grams. It was used in shop window displays and nothing about it was functional. It was beautiful, made completely out of stainless steel with a detachable head that you could put in your backpack. The blade was 8mm thick, smooth and totally useless.
My second ice axe showed that I had evolved as a designer. Its weight and size were inspired by the first quark ergo that I had seen in some footage. Two days later I would have my first and only waterfall climbing course lesson held by the CAI of Mantova and I wanted to come with my very own ice axes. They were made of three layers of 8mm ergal, blade included. Shaped just as I had designed, great to look at, weight 800 grams. The instructors gave it a look over, asked me to hit a wall of ice, along the route of the Daone Valley, with it. I did. It vibrated for a second or two... the ice axe failed miserably. Unanimous decision.
The next course was to take place a year later. That meant I had a year to design something good and regain my reputation... it was a challenge. I also got to decide which materials I would use.
The choice of materials is the part I like best about designing. Choosing the materials for something you actually get to use is great. One thing was certain; the ice axe and grip had to be a lot lighter and I had to make the blade heavier. The first solution was to mount commercial blades onto hand-made grips... a low cost, mediocre result but the ice axe worked. I was unwittingly now a part of the group of ice climbing enthusiasts who, even more than rock climbers, have a variegated and extremely precise vocabulary and a real obsession for the "first tooth" which always needed anther filing... I surfed the internet and on Bubu's site I saw that he modifies the stuff he buys. And so I sent him an email to ask him what he thought of what I'd done and although he didn't sound too thrilled he did seem interested in a few of the strange things I had made.
He wrote back to me a few months later and arranged a meeting where we could throw down some ideas. A few evenings in front of the computer and a few years later I look back on what we've achieved and I'm rather happy about how thins have turned out.
What we've done is kind of magical...nothing impossible but profoundly satisfying.
Having the opportunity to work with materials classified as "composite" opens many doors in terms of design and realization which traditional manufacturing with metal alloys doesn't.
The opportunity of working with high-resistant steel to create small objects like a blade is, in some ways, a privilege. The amount of material used to create a blade is reduced by a few hundred grams and however high the cost of material may be at the outset, the advantage in terms of weight is extraordinary. As a result we chose the material that we thought was the best without giving much thought to the expense. The process is fiddly due to the small size of the tool but still not fiddly enough not to be hand-made which is how we prefer things to be done... but then again wasn't spending hours in front of a piece of metal and increasing its value the dream of alchemists?
Our little magic act lies in putting a grip in a composite material together with a high-resistant ferrite steel blade, protect some parts using a light-weight alloy and accessories in titanium making our product a concentrated mix that is totally new and never seen before.
Maybe the fact that we didn't have anything prepared gave us the freedom to choose the materials we though were best as well as the best process for every part by working with friends and collaborators whose passion helped us solve the small problems we met along the way. And so, there are lots of people I would like to thank.
First of all I'd like to thank my father who gave me a Meccano at the age of 5 which helped me along my way of working with metals.
Avio Brancato whose brilliant ideas often helped me solve apparently impossible mechanical problems. The lathe of the Di Padova brothers who always manage to fix the mistakes I make.
Ivan, Gianangelo and Claudio of Comav Technology who with their enthusiasm, experience and time made the composite parts.
And most of all I'd like to thank Bubu who is made for this line of work. Only he has the experience to assess which modification is The One, making the whole climb-design-prototype process extremely fast.
Stefano
PRODUCTION
I think... actually, I'm convinced...that it's right to take risks...no safe life for me! Take the risk and try to make your dreams come true! At times it works, other times it doesn't... but as they say, "if you don't try, you won't succeed"... believe in yourself... you can't lose!
It's true... it depends on your character too... I don't know whether it's luck but I'm stubborn and I never give up... I can't help it but I have to try!
In the last few years I've become very demanding of mixed modern equipment. I've spent many hours in my basement cutting, soldering and modifying equipment but I got to a certain point where I found the need to put all my 25 years of climbing experience into practice.
There are few companies in this field that try to satisfy the needs of the true climber. This is because in order to make good equipment you either have to use it or listen to the advice of people who really do know how to use the equipment... that's why manufacturers always fall into the trap of making low-cost equipment for the mass market. This way of thinking though isn't enough for demanding experienced climbers who require equipment that works and is safe!
I'm one of those people... demanding... who expects the most from himself and from his equipment. I think it's the best and most intense way to live life!
In 2003 I received an email from Stefano Azzali of Mantova. A passion for the mountains, a professional welder and most importantly a metallurgy fanatic, he showed me some of his products (ice axes) that he'd made in his free time!
He asked my opinion and I replied that his ice axes were rubbish! I didn't mean to offend him but then again it was my opinion! On the other hand his photos did leave their mark - the imagination and creativity put into the tools were not to be found on the market.
And so it was luck that we met and together we mixed his manual ability and my experience.
I'll never forget spending all those hours in front of his PC. On paper I drew the ice axes I had designed in my brain over the years and he reproduced them into 3D images on screen with incredible speed and precision.
Hours and hours of drawing and redesign until we gave shape to our ideas... first in metal and then the decision to use carbon which would help to realize our dream tool.
We then met Ivan Guerinoni and Gianangelo Roosi of Comav Technology who had the courage to try to put our designs into practice.
We had found two other headstrong people whose great experience and stubbornness turned out ergonomic, lightweight, resistant and beautiful carbon ice axe handles that were very, very difficult to make!
How satisfying it was for all of us!
PASSION, MOTIVATION and CREATIVITY are three words that recall our mutual madness... and it had seemed all so impossible!
To conclude, the positive results of the resistance tests held by TUV product service for international product c ertifications has inspired us to design other products. It is important to make all climbers happy! First of all, me!
Heartfelt thanks to Stefano, Ivan and Giana who supported me and kept my feet on the ground... and continue to keep me on a leash (as much as possible anyway)...
Bubu
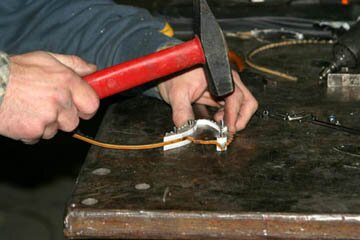
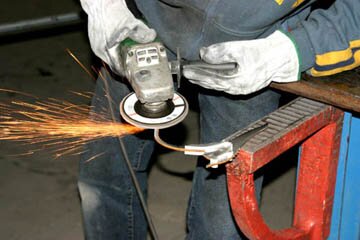
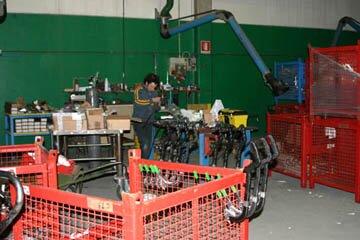
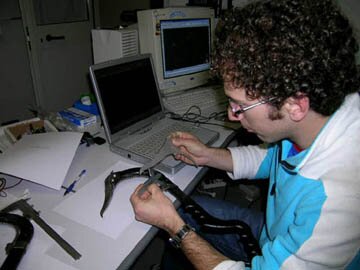
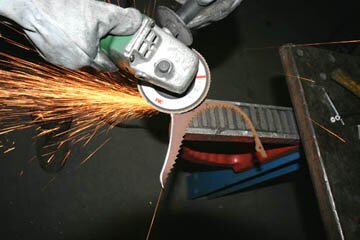
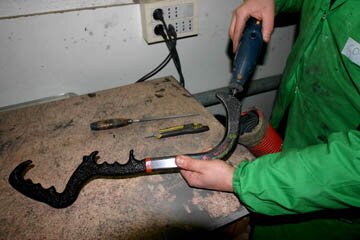
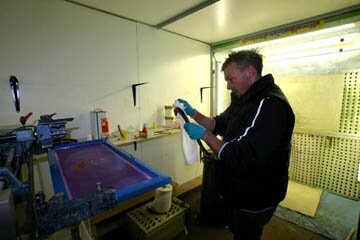
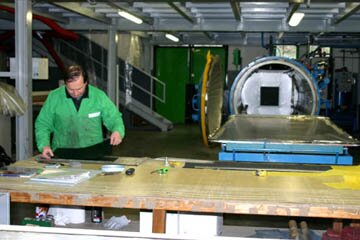
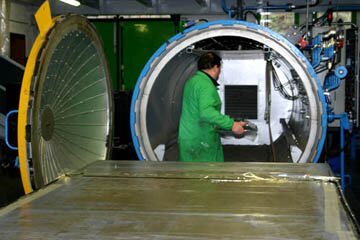
|
|
 |
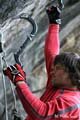
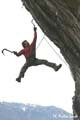
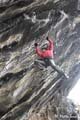
|